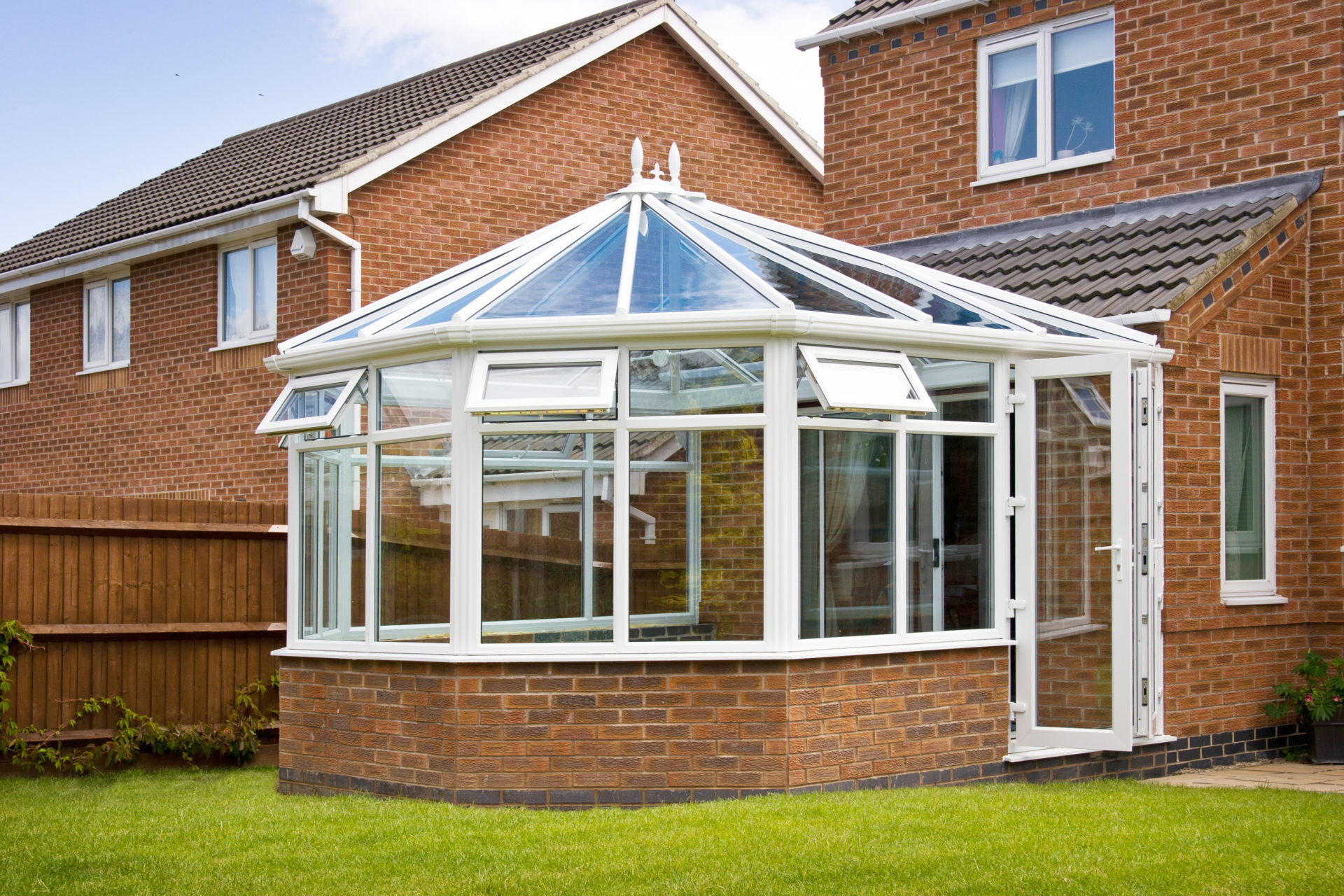
Durabase Extensions & Conservatories.
DurabasePlus 100 for Extensions, Conservatories, and Porches!
Durabase Conservatory
Durabase Conservatory offers a more straightforward and cleaner method for constructing the foundation base for your new conservatory or extension; below is what we must do for a typical build.
Traditional Building Methods
This is the same application for an Extension, Conservatory, Orangery or Porch.
The initial phase of a Conservatory installation entails removing the existing patio, Concrete slab, and soil and clearing the perimeter around the exterior to a depth of 250mm below the existing damp course, approximately equivalent to three bricks deep. Before constructing the conservatory, it is important to measure the perimeter to a size slightly larger than the intended finished dimensions.
To accommodate the new base brickwork, we need to excavate a trench that is 600mm wide and 1 meter deep. This can be done manually or with a mini digger. After the excavation, we should fill the trench with C25 concrete, typically pumped in through the house or a side gate if accessible. If there are nearby trees, it’s advisable to dig the trench to a depth of 1500mm to 1800mm, depending on the proximity of the roots and soil type. This will require additional labour and concrete costs.
Typical Base Requirements
U-Value = 0.18W/m²K: 150mm of compacted MOT type 1 hardcore, 50mm of sand blinding, 1200 DPC Vis-queen sheeting for DPC, 150mm floor insulation, 100mm concrete leaving 70/80mm for screed at the end of the build.
Building the structure, U-Value = 0.18W/m²K Bricklayer will install a double skin wall to damp course height. Approximately 225mm high to existing damp proof (DPC) using red or blue class B engineering brick. 102mm Face brick to match existing or choose from a sample you like, 150mm cavity with Brickwork, insulated with a thermal conductivity of 0.032 W/m²K, 100 mm block work with a thermal conductivity of 0.15 W/m²K 12.5mm plasterboard finish to achieve minimum requirements.
Southeast Windows is the ideal partner for purchasing and installing the Durabase modular system is especially suitable for terraced homes without side access. Durabase has a 25-year manufacturer’s guarantee and BBA approval, ensuring long-lasting quality.
Conservatory Building Regulations Guidelines
Conservatories are usually exempt from building regulations under Permitted Development Rights if they satisfy the following conditions:
- Built at ground level with a floor area of no more than 30 square meters.
- 50% of the new wall and 75% of the roof must be glazed or made of translucent material.
- External walls or windows must separate the conservatory from the house.
- The glazing and any fixed electrical installations must comply with applicable building regulations.
- The heating system must be independent of your home, with separate temperature and on/off controls.
- The level of glazing in the original home’s roof, windows, and doors cannot exceed 25% of the floor area of both the home and conservatory combined.
- The glazing in the conservatory’s roof, windows, and doors cannot exceed 25% of the conservatory’s floor area.
- Doors and windows must adhere to current U-Values.
- All glazing in doors and windows must be toughened or laminated safety glass, meeting British Standard 6206.
Efficient and Space-Saving Design
Traditional building methods usually require a 150mm cavity for insulation, with walls needing about 250mm of internal space. DurabasePlus 100 uses a galvanised metal carcass box with pre-fixed brick slips, reducing the internal wall size to 173mm. This design improves energy efficiency, lowers heating bills, and helps reduce your carbon footprint, making it an excellent choice for green home improvements.
New Building Regulations
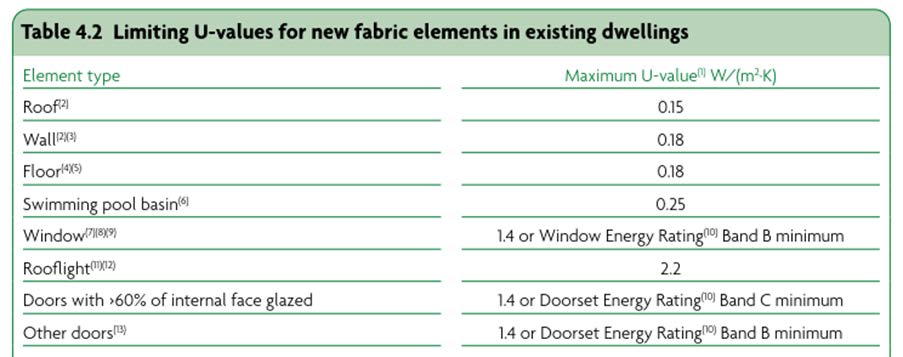
As of June 15, 2022, England’s building regulations now require improved U-values for thermal elements. The DurabasePlus 100 system meets these new regulations, allowing for quick construction on padstone foundations.
Less Mess, Less Waste
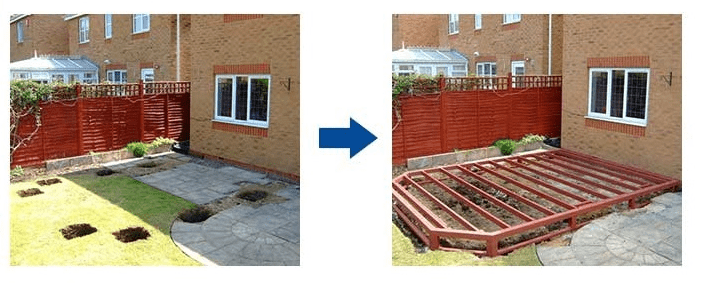
The Durabase Conservatory, built with the DurabasePlus 100 system, arrives in a kit that minimises excavation. We strategically place 450 x 450 x 450 concrete pads to avoid the need for deep footings and excessive waste. We backfill the padstones with C40 Concrete pre-mixed in bags, using an average of 10 bags per hole.
Laying the Base
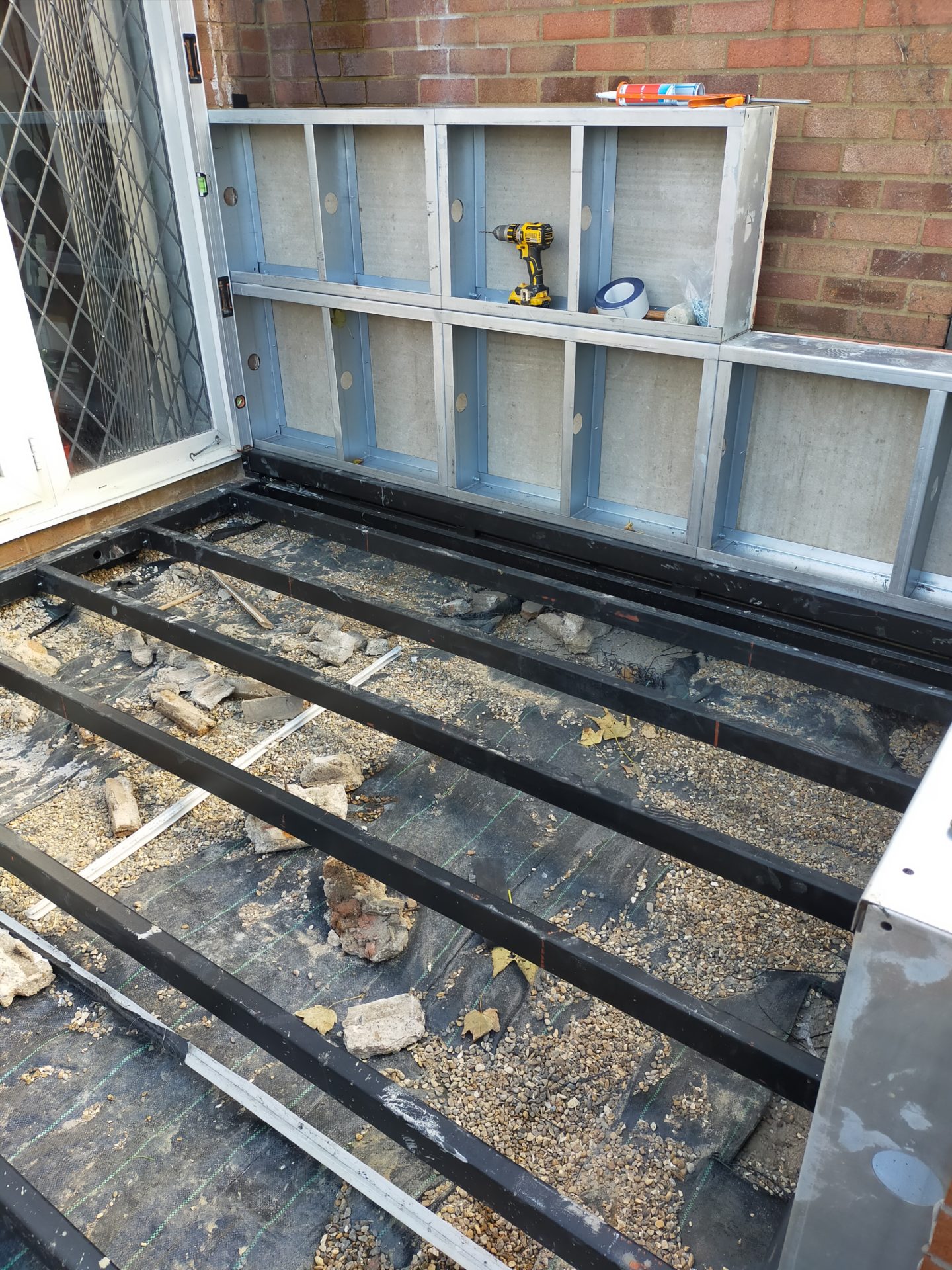
Our process begins with clearing the base area below the existing DPC and laying down a heavy-duty weed barrier. The steel base is then installed and levelled. The galvanised brick carcass frame follows, with 100mm PIR insulation in the floor and 200mm insulated walls.
Brick Skirt
Installation of the steel base involves adjusting the internal legs to confirm its level, followed by adding a cement board skirt around the perimeter, typically 250mm below the house’s existing DPC. Genuine clay brick tiles bond to these boards, creating a durable yet lightweight wall system in various colours and textures from the Britannia brick range. Brick mortar comes in three colours: Red, Grey, and Sandstone. Air bricks are installed around the base to ensure proper airflow, which is essential for homes with floorboards.
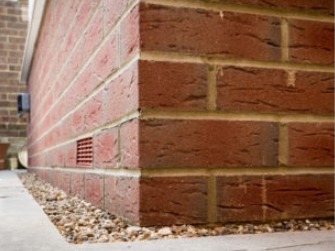
Durabase Conservatory modular walls feature a sturdy galvanised frame with profiled insulated building boards tailored to your conservatory’s size and shape.
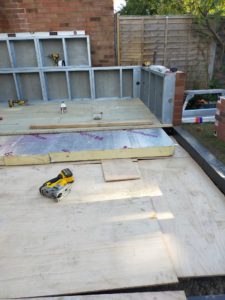
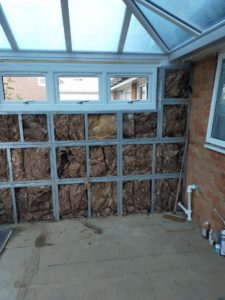
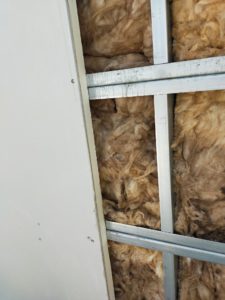
The Durabase Conservatory picture shows a double Edwardian roof and a fire-rated wall ideal for a TV.
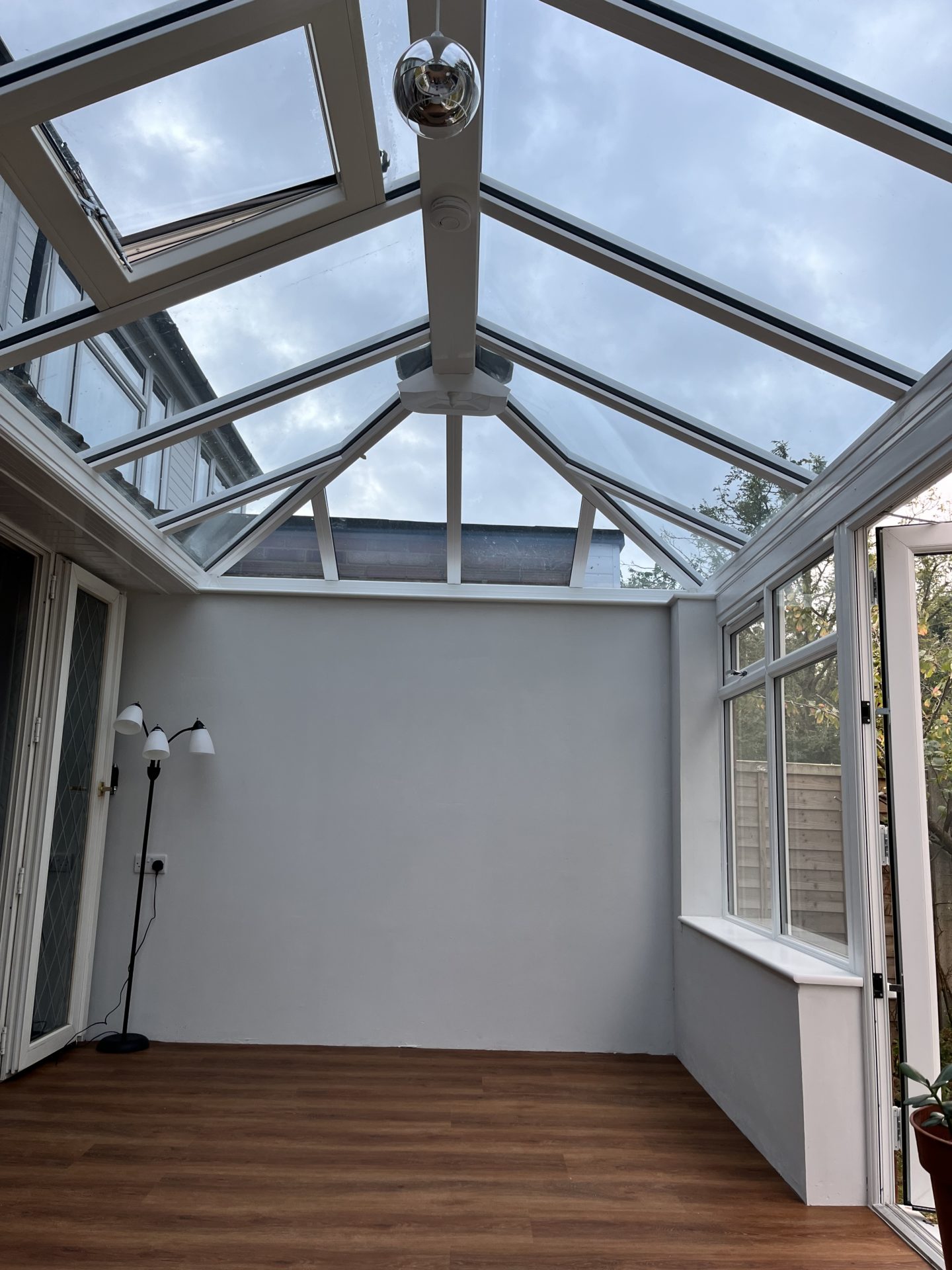
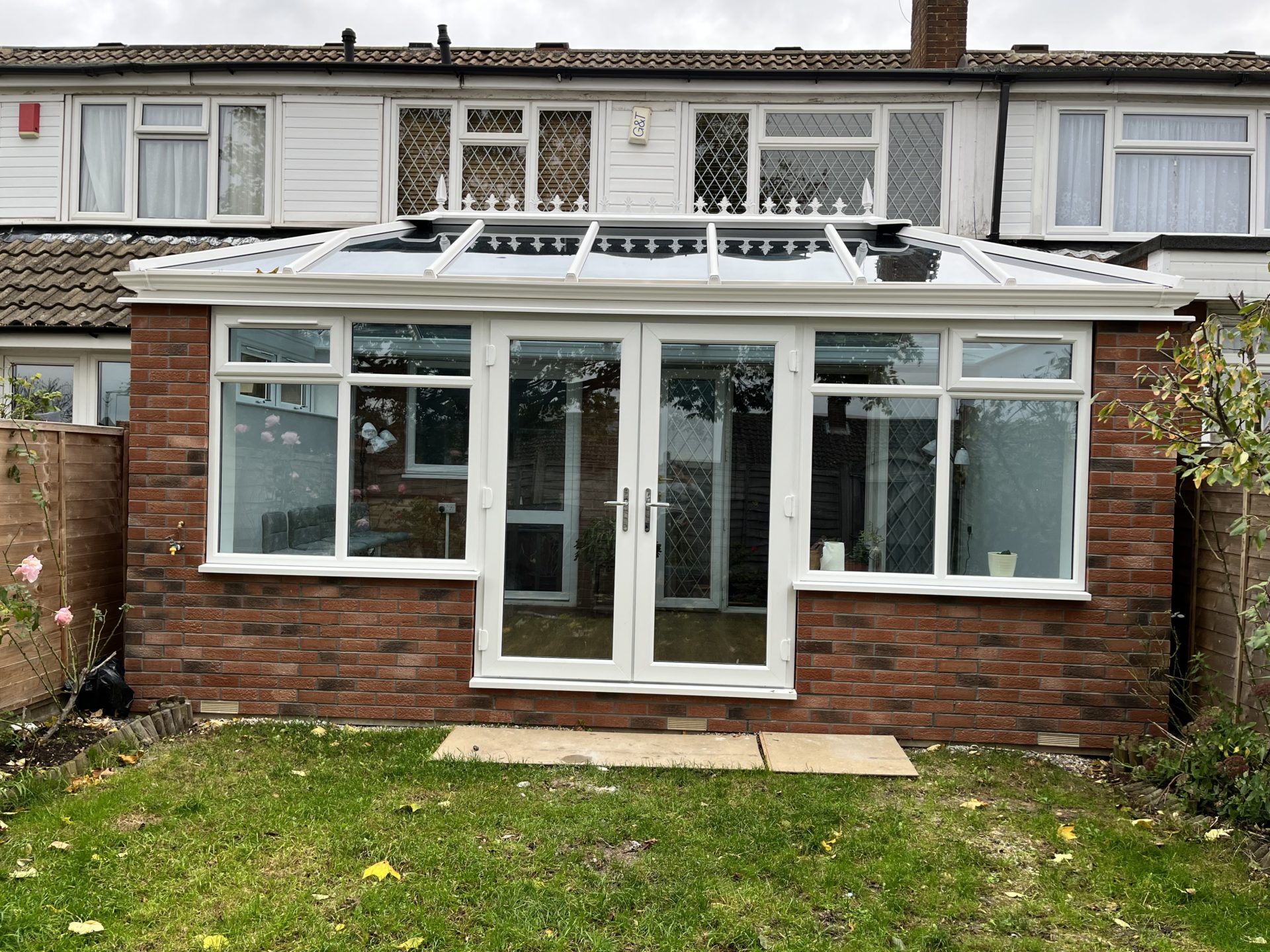
The construction project included installing a DurabasePlus100 base and a Conservatory featuring two fire-rated walls adjacent to the neighbouring property and French Doors at the front. At the rear, a box gutter was installed along the back wall to manage rainwater runoff from the roof. Notably, the Conservatory showcases a double Edwardian glass roof with Pilkington’s blue self-cleaning glass.
Cost-Effective Solution
Building regulations require contacting your sewerage company if you plan to build near a public drain. Traditional concrete foundations don’t allow you to build over manholes, but the DurabasePlus 100 system offers an alternative option. With a cutout in the steelwork for drain access, this system includes a double-seal inspection chamber, saving costs and simplifying the build process.
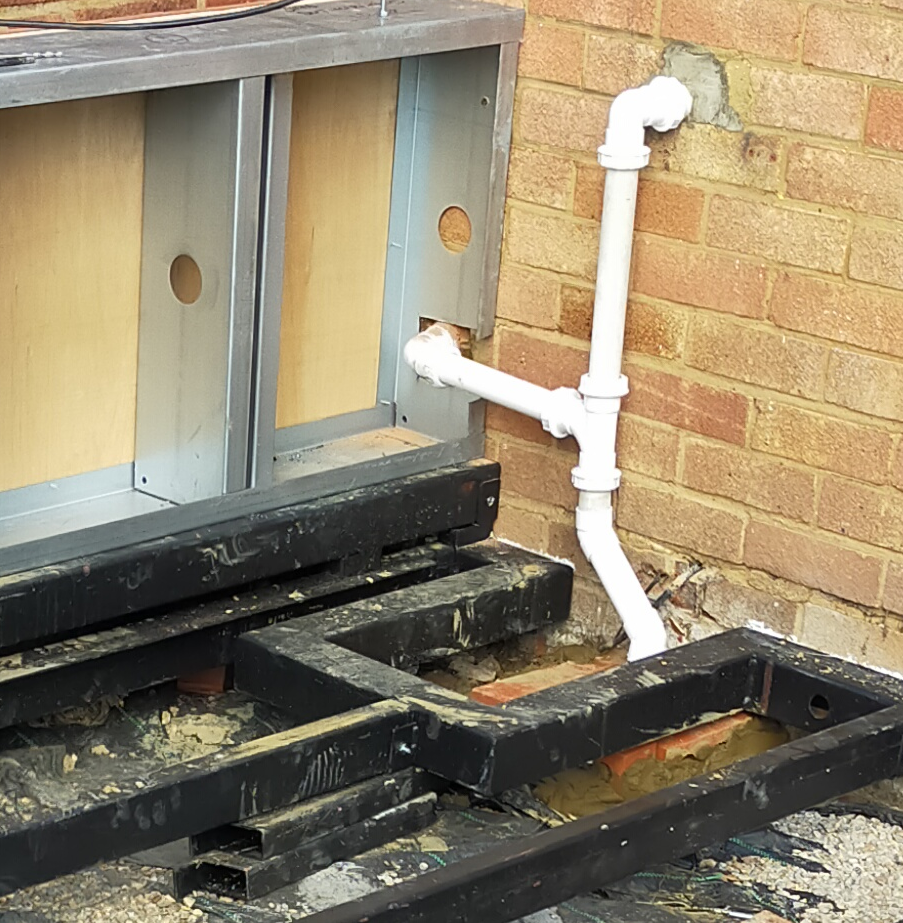
The DurabasePlus 100 steel base features a drain cutout designed to accommodate an external drainpipe. In a conventional base construction, this feature would need to be extended to the exterior of the base.
The same cut-out was completed, showing the finished floor and double-seal drain cover.
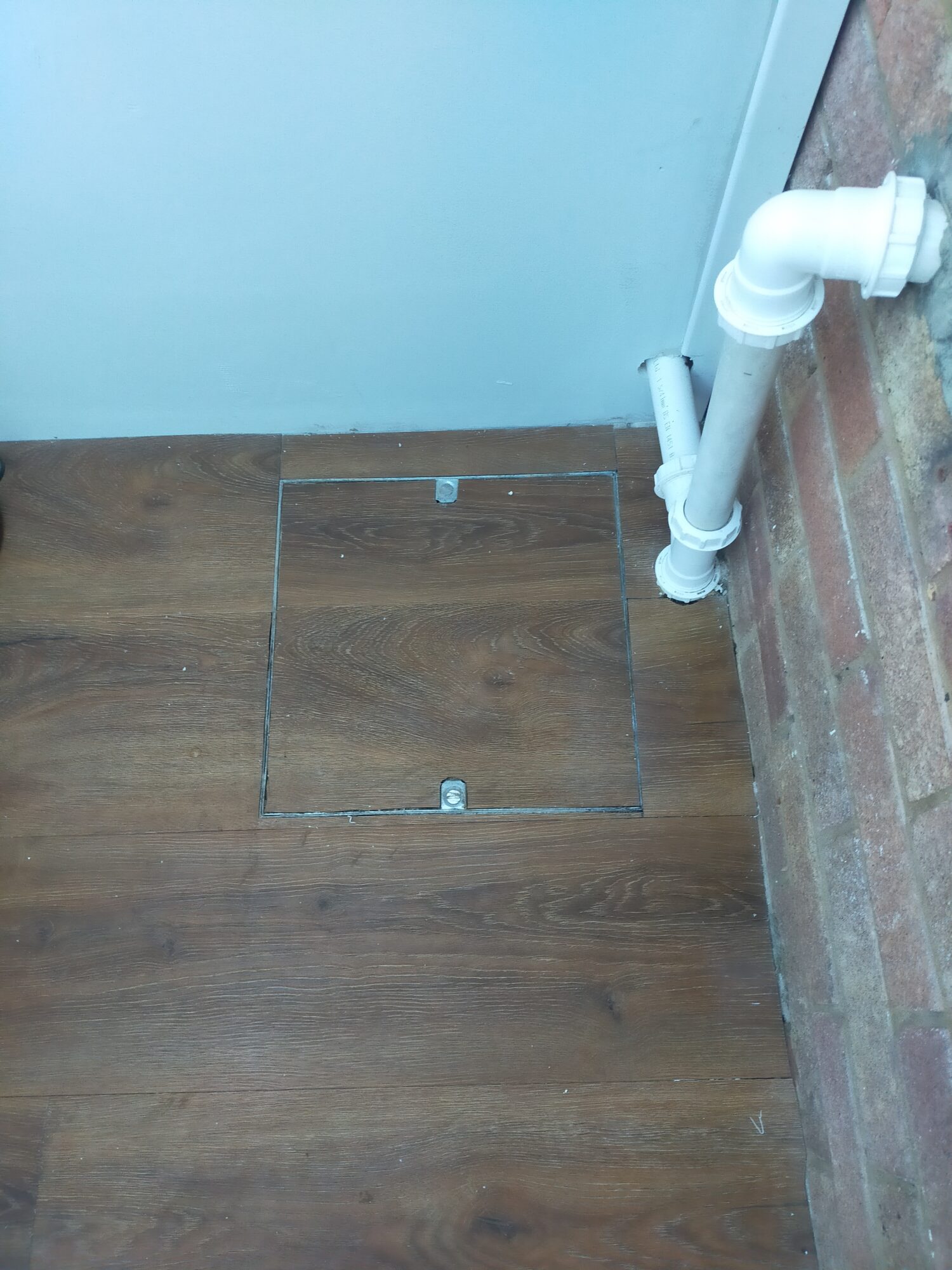
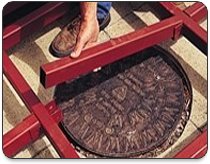
A removable steel framework to cover the drain access panel, specifically designed for easy maintenance access from the inside, is well-suited for use in Extensions and Conservatories where the external drain must be relocated beyond the construction area for access.
Building Regulations
Stroma Building Control ensures that all projects meet the latest building regulations. Independent inspectors oversee every stage, ensuring compliance. After completion, you receive a certificate that proves your project meets all building regulation requirements.
Want to know More?
Call us today for your FREE, no-obligation quotation or fill out our Contact Form! For the most modern, energy-efficient replacement Windows, Doors and Conservatory with a 10-year Insurance Backed Guarantee for complete home Comfort & Designed to Keep You Warm, Safe, & Secure.
Alternatively, call your local number below to arrange an appointment.
East London Durabase: 020 8472 4088 (head office)
South London Durabase: 0203 856 6667
North London Durabase: 0203 856 6669
Chelmsford Durabase: 01245 208 058
Romford Durabase: 01708 202 457
Great Dunmow Durabase: 01371 704 771